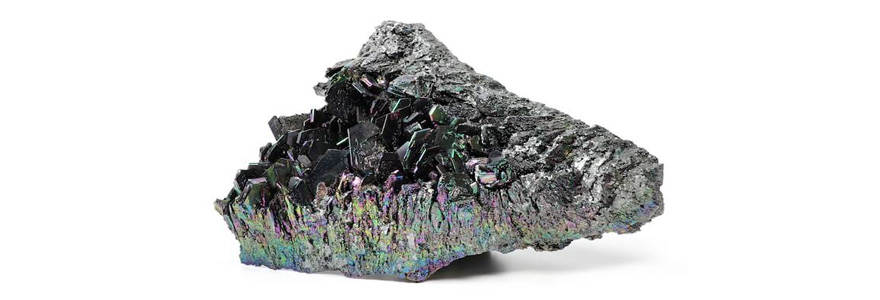
Dans l’industrie électronique, les wafers en silicium sont devenus essentiels en tant que supports de microstructures. Leur fabrication nécessite différents procédés et traitements que seules les entreprises spécialisées peuvent réaliser.
En quoi consiste un wafer ?
Ce terme qui vient de l’anglais réfère à une plaque métallique très fine à base d’un matériau semi-conducteur (par exemple du silicium). Les wafers silicium sont surtout utilisés pour fabriquer des substrats de Silicium et des membranes de Silicium. Ils servent également à la fabrication de microstructures destinées à des techniques comme la gravure, le dopage, la photolithographie ou dans les opérations de déposition d’autres matériaux (dépôt chimique en phase vapeur, sputtering, épitaxie…). C’est aussi une composante importante dans la fabrication des cellules photovoltaïques, des transistors, des circuits intégrés, des semi-conducteurs de puissance et des micro-capteurs MEMS.
Quelles en sont les caractéristiques ?
Les wafers sont produits en différents formats (de 25,4 mm à 300 mm, pour une épaisseur de 0,7 mm). Pour souligner l'orientation des plans cristallins, on y retrouve généralement une marque sous forme d’encoche ou d’un méplat sur le côté (dans le cercle). Les transistors, circuits intégrés et semi-conducteurs de puissance sont imprimés sur ces wafers sous forme d’un quadrillage serré pour en regrouper un maximum sur une seule surface.
Comment sont produits les wafers Silicium ?
La fabrication des wafers exige du silicium de qualité métallurgique, soit 98% de pureté ; pour obtenir ce résultat, il faut réduire du sable quartzeux avec du carbone en utilisant un four (température de plus de 1900°C) à arc électrique. La majeure partie des wafers produits (90%) est consacrée à la fabrication des cellules solaires (mono et polycristallines), alors que le volume restant est utilisé dans l’industrie des semi-conducteurs. En raison de la concentration d’impuretés présente dans le silicium, celui-ci doit être purifié et transformé en trichlorosilane gazeux (à l’aide d’acide chlorhydrique). Avant d’être décomposé thermiquement en silicium polycristallin, le trichlorosilane subit une distillation multiple pour en optimiser la pureté à 99,999…%. Ce procédé de formation du silicium polycristallin est réalisé selon la méthode de Siemens. Pour produire un monocristal à partir du silicium fondu, la technique de croissance des lingots de silicium monocristallin par la méthode Czochralski peut être privilégiée. Celle-ci permet d’obtenir des cristaux de plus grand diamètre (46 cm) et de réduire le coût de production des wafers.
Découpe et autres étapes de finition
Découpage, rodage, laminage, polissage et nettoyage constituent les étapes de finition des wafers. Pour la découpe, les techniques les plus courantes sont la scie à fil et la scie annulaire. Avec la scie à fil, chaque lingot se déplace rapidement en produisant une tension sur les fils en mouvement puis il est découpé en wafers individuels. Dans la technique avec la scie annulaire, les wafers sont sciés à l'intérieur d'une lame circulaire diamantée. Cette opération leur donne une bonne planéité et une rugosité facilitant l’étape suivante : le rodage. Une fois la découpe terminée, les wafers doivent être rodés des deux côtés. Cela sert à éliminer le rayures, fissures et autres défauts de la surface. Elle permet aussi d’amincir le wafer jusqu'à l’épaisseur désirée. Une opération de laminage, à l’aide d’agents de gravure, suivie d’un polissage des wafers puis d’un nettoyage les rendra lisses et prêts à la distribution.